How Can You Do Simple DIY Repairs for Your VLF Detector?
Very Low Frequency (VLF) detectors are key tools for many tasks. They help with radio frequency analysis and military communications. Even though they’re bui
lt to last, sometimes they need a little fix. Luckily, many issues can be solved with simple DIY repairs, saving you money on professional services.This guide will cover common VLF detector problems. You’ll learn how to deal with signal interference, coil sensitivity, and power issues. You’ll discover how to troubleshoot, what tools and mate
rials you need, and how to fix things at home. Knowing how your VLF detector works can help it last longer, work better, and save you money.If you’re into hobbies, research, or work with VLF technology, this article is for you. It will give you the skills to fix common problems with your VLF detector yourself. Let’s get started and learn how to keep your VLF detector in top shape.
Understanding Common VLF Detector Issues
Using very low frequency (VLF) detectors helps with electromagnetic spectrum monitoring and signal processing techniques. But, users often face several common problems. These issues can affect how well these devices work. It’s important to solve these problems to keep VLF detectors reliable and accurate.
Signal Interference Problems
VLF detectors can pick up interference from things like electrical noise and radio waves. Even nearby metal can cause problems. This can lead to wrong readings, false signals, or a drop in sensitivity. It’s key to find and fix these issues for consistent VLF detection.
Coil Sensitivity Issues
The coil’s sensitivity is a big deal for VLF detectors. Damage, bad shielding, or loose connections can lower sensitivity. This might cause false signals or make it harder to detect things. Keeping the coil in good shape is vital for reliable VLF detection.
Battery and Power Concerns
Good power management is essential for VLF detectors. Problems with batteries or power can lead to poor performance or even stop the device. It’s important to check battery levels, use quality batteries, and follow the right power management steps.
Knowing and fixing these common VLF detector problems helps users get the most out of their devices. Regular care, troubleshooting, and solving problems early on can help avoid these issues. This way, VLF detection technology can reach its full potential for accurate electromagnetic spectrum monitoring and reliable signal processing techniques.
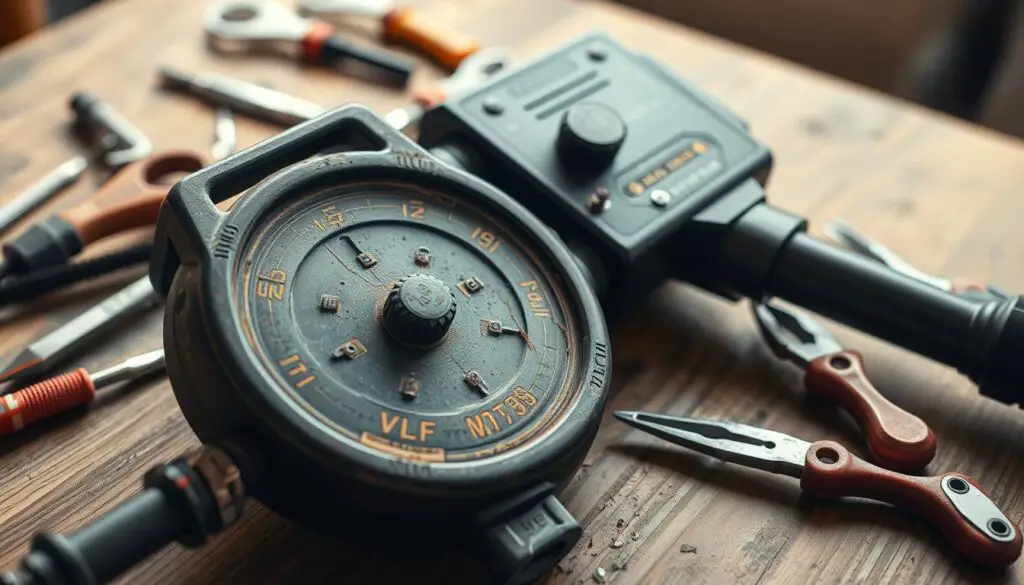
Essential Tools and Materials for VL Frequency Detector Repairs
Fixing your VLF (Very Low Frequency) detector needs the right tools and materials. These items help you find and fix problems with your wideband frequency scanning or signal intelligence device.
You’ll need a soldering iron, solder wire, and a multimeter for repairs. Wire strippers, screwdrivers, and pliers are also crucial. They let you work on the small parts and connections inside your detector.
You might also need replacement wires, conductive epoxy, and heat shrink tubing. For coil repairs, a heat gun, sharp knife, and special glue are needed. You might also need extra parts like capacitors, resistors, and switches for circuit problems.
Keeping your VLF detector in good shape is important. With the right tools and materials, you can quickly find and fix issues. This keeps your wideband frequency scanning and signal intelligence working well.
Essential Tools | Necessary Materials |
---|---|
|
|
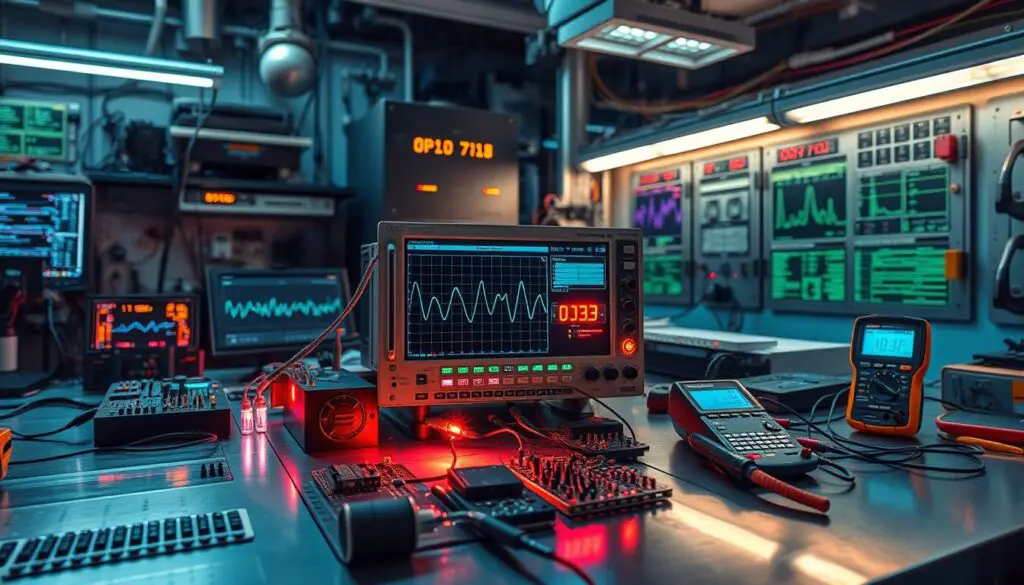
Troubleshooting Faulty Coil Connections
Fixing coil connection problems is key to keeping your VLF detector working well. Bad connections can mess up radio wave propagation and lower your device’s sensitivity. Let’s look at some common issues and how to fix them.
Checking Solder Joints
First, check the solder joints where the coil meets the detector’s cables. Look for signs of dryness, cracks, or breaks, especially at the plug. A magnifying glass can help you see these spots better. Fixing any bad joints can fix the electrical flow.
Testing Wire Conductivity
Then, test the wires in the coil cable for conductivity. Use a multimeter to find any wire breaks or damage. This step helps spot internal issues that might cause signal problems. Replace any bad wiring to keep your spectral analysis tools working right.
Identifying Shielding Problems
Coil shielding stops electromagnetic interference. Check the Faraday shielding inside the coil for loose or oxidized wires. Use a multimeter to check the shielding’s continuity and resistance. Clean and fix any oxidation and wires to keep the signal clear.
By tackling these common coil connection issues, you can fix many problems with your VLF detector. Keeping the coil and wiring in good shape is vital for reliable radio wave propagation and spectral analysis tools use.
Repairing the Detector’s Electrical Components
Keeping your spectrum monitoring systems or VL Frequency Detector in top shape often means fixing the electrical parts. This might mean swapping out or fixing circuit board pieces like the 555 timer IC, resistors, capacitors, and the buzzer or speaker.
Before you start fixing parts, make sure you know the layout of your device’s circuit. This is crucial for making the right connections. If you built your VL Frequency Detector yourself, testing the circuits on a breadboard before soldering can be super helpful.
- Double-check your connections and pick the right values for resistors and capacitors.
- Think about using better components for better performance.
- Be gentle when removing or replacing parts to avoid damaging the circuit board.
By carefully fixing the electrical parts of your spectrum monitoring systems, you can make your device last longer. It will also keep working well. Remember, being careful and methodical is key to fixing things right.
Advanced Coil Maintenance and Replacement Techniques
If you love using a very low frequency (VLF) metal detector, keeping the coil in good shape is key. This includes taking it apart and replacing wires. We’ll show you how to keep your VLF detector working great.
Coil Disassembly Methods
Start by taking the coil apart carefully. Warm it up with a heat gun to loosen any glue. This makes it easy to remove the windings and see inside without harming it.
Shielding Wire Replacement
The shielding wires in your coil are important for avoiding interference and getting accurate readings. Choose non-magnetic wires like Nicrome, about 0.32mm thick. This keeps your coil’s performance strong.
Reassembly Best Practices
After fixing or changing things, put the coil back together. Mix melted skid plate pieces with acetone to glue it. Make sure it’s sealed well to keep moisture out. For DIY coils, aim for 10 mH inductance and use the right wire and turns.
Conclusion
Fixing your VLF detector yourself can save money and keep it working well. You can solve many problems like signal issues and power problems on your own. But, some complex issues might need a pro.
Having the right tools and following repair steps carefully can help fix many problems. You can fix coil issues and electrical parts safely. But, replacing advanced parts needs extra skill and care.
DIY repairs can be rewarding and cost-effective. Yet, knowing your limits is key. For tough problems or expensive detectors, getting help from a pro is wise. This way, you balance DIY fixes with expert advice, keeping your VLF detector in top shape.